In the realm of industrial piping and valves, selecting the appropriate bolts to hold everything together is critical to ensuring system integrity, safety, and longevity. Among the options available, A4 bolts, A2 bolts, and zinc coated 8.8 bolts stand out for their unique properties and specific applications. This blog post will delve into the differences between these bolts and their respective usage in industrial settings.
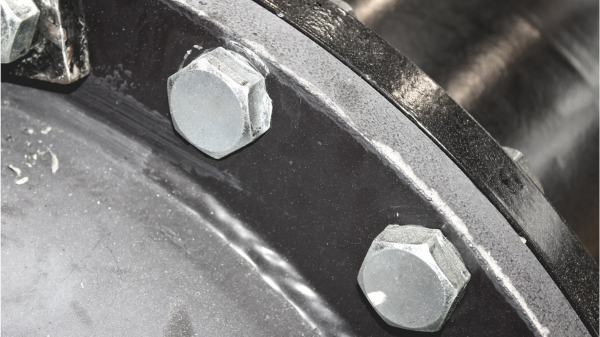
A4 Bolts
Composition and Properties:
A4 bolts are made from A4 stainless steel, also known as 316 stainless steel. This alloy contains molybdenum, which enhances its corrosion resistance, especially against chlorides and other industrial chemicals. 316 stainless steel is considered ‘food grade’. This allows it to be used in the likes of potable water and food factories.
Characteristics:
- Corrosion Resistance: Exceptional, especially in marine environments or where exposure to chlorides is a concern.
- Strength: Comparable to A2 bolts, suitable for moderate to high strength requirements.
- Temperature Resistance: Maintains structural integrity and corrosion resistance at high temperatures.
Usages:
- Marine Applications: Ideal for use in marine environments due to their high resistance to saltwater corrosion.
- Chemical Processing: Suitable for industries involving harsh chemicals, ensuring durability and safety.
- Food and Beverage: Their non-reactive nature makes them ideal for environments requiring high hygiene standards. The 316 stainless steel used is considered ‘food grade’ and any application that comes in contact with potable water must use this type of steel/ bolt.
A2 Bolts
Composition and Properties:
A2 bolts are made from A2 stainless steel, commonly known as 304 stainless steel. This alloy contains chromium and nickel, providing a good balance of strength and corrosion resistance.
Characteristics:
- Corrosion Resistance: Good, but not as high as A4 bolts. Suitable for general outdoor use and mildly corrosive environments.
- Strength: Adequate for many industrial applications, though slightly less than A4 bolts.
- Temperature Resistance: Performs well under a range of temperatures but is not as resistant as A4 in extreme conditions.
Usages:
- General Industrial Applications: Used in a variety of settings due to their versatility and cost-effectiveness.
- Outdoor Installations: Suitable for environments exposed to weather but not extreme marine or chemical exposure.
- Construction: Often used in building structures and general infrastructure due to their balance of strength and resistance to corrosion.
Zinc Coated 8.8 Bolts
Composition and Properties:
Zinc coated 8.8 bolts are carbon steel bolts that have been coated with a layer of zinc to enhance corrosion resistance. The “8.8” grade denotes a high tensile strength, typical of medium carbon steel.
Characteristics:
- Corrosion Resistance: Enhanced by the zinc coating, making them suitable for outdoor and mildly corrosive environments. However, they are not as corrosion-resistant as stainless steel bolts.
- Strength: High tensile strength, suitable for heavy-duty applications.
- Temperature Resistance: Performs well under moderate temperature conditions but can degrade under high heat or extreme environments.
Usages:
- Heavy Machinery: Ideal for use in securing heavy equipment and machinery due to their high tensile strength.
- Outdoor Structures: Commonly used in construction and infrastructure projects where moderate corrosion resistance is sufficient.
- Automotive Industry: Frequently used in the automotive sector for their strength and reasonable corrosion resistance.
Choosing the Right Bolt for Your Application
Selecting the appropriate bolt for industrial piping and valve hinges is key. Therefore understanding the specific requirements of your application is a must. Here’s a quick guide to help:
1. Environment:
- A4 bolts are best for marine or highly corrosive environments.
- Opt for A2 bolts for general outdoor and mildly corrosive environments.
- Use zinc coated 8.8 bolts where corrosion is less of a concern and strength is paramount.
- If any of the bare steelwork is coming in contact with any potable water or other food and beverage application it will need to use A4 bolts due to them being made of 316 stainless steel, which is considered ‘food grade’.
2. Strength Requirements:
- Zinc coated 8.8 bolts are best for applications demanding high tensile strength.
- Both A4 and A2 bolts offer good strength but are more balanced with corrosion resistance.
3. Cost Considerations:
- A2 bolts are generally more cost-effective than A4 bolts.
- Zinc coated 8.8 bolts provide a cost-effective solution for high-strength requirements where extreme corrosion resistance is not needed.
Conclusion
Understanding the differences between A4 bolts, A2 bolts, and zinc coated 8.8 bolts allows for informed decision-making in industrial piping and valve applications. By considering factors such as corrosion resistance, strength requirements, and cost, you can ensure the longevity, safety, and efficiency of your installations.
Whether dealing with the harsh conditions of marine environments, the demands of chemical processing, or the structural requirements of heavy machinery, there is a suitable bolt for every application.